在生物制药生产中,一个直径仅0.1毫米的微孔或一道0.01微米的表面划痕,都可能成为微生物滋生的温床,直接导致价值数百万美元的药品批次报废。
生物制药专用阀门作为流体控制系统的核心组件,通过材料革新、结构优化与智能控制三大技术突破,构建起覆盖全流程的无菌屏障,成为保障药品质量与生产安全的“隐形守护者”。
1.超洁净材料:从分子层面阻断污染
生物制药阀门主体采用316L不锈钢或聚四氟乙烯(PTFE)等惰性材料,其表面经过机械抛光(Ra≤0.25μm)与电解抛光(Ra≤0.1μm)双重处理,较工业阀门降低80%的表面粗糙度。某德国品牌隔膜阀通过在316L阀体内衬0.5mm厚PTFE涂层,将蛋白吸附率从0.5mg/cm2降至0.02mg/cm2,成功应用于单抗药物生产。密封件则选用符合USP Class VI标准的EPDM或FFKM橡胶,经伽马射线灭菌后拉伸强度保持率>95%,确保长期密封可靠性。
2.360°流道:消除交叉污染风险
传统阀门90°弯角处的流体滞留区是微生物滋生的重灾区。生物制药阀门创新采用全通径或斜角流道设计,配合CFD模拟优化技术,将残留体积从1.2ml降至0.05ml。某无菌级球阀通过流道优化,使细胞培养基残留率降低98%,显着降低批次间交叉污染风险。三通抗生素截止阀更以螺旋流道与双重关闭设计,实现零死角、零泄漏,在抗生素发酵工艺中染菌率降低至0.003%。
3.智能控制:精准驾驭生命流体
在细胞培养基补料环节,微型针阀通过压电陶瓷驱动技术,实现0.1-10ml/min的精准投料,流量重复性误差<±0.5%,避免营养失衡导致的细胞凋亡。某多通道分液阀集成双密封圈与自排水结构,确保121℃高温灭菌蒸汽100%穿透流道,灭菌验证符合FDA 21 CFR Part 11要求。更值得关注的是,模块化设计使阀门可与一次性生物反应器、层析系统无缝对接,某品牌无菌取样阀采用Luer锁接口与预灭菌包装,单次使用成本降低40%,安装时间从2小时缩短至15分钟。
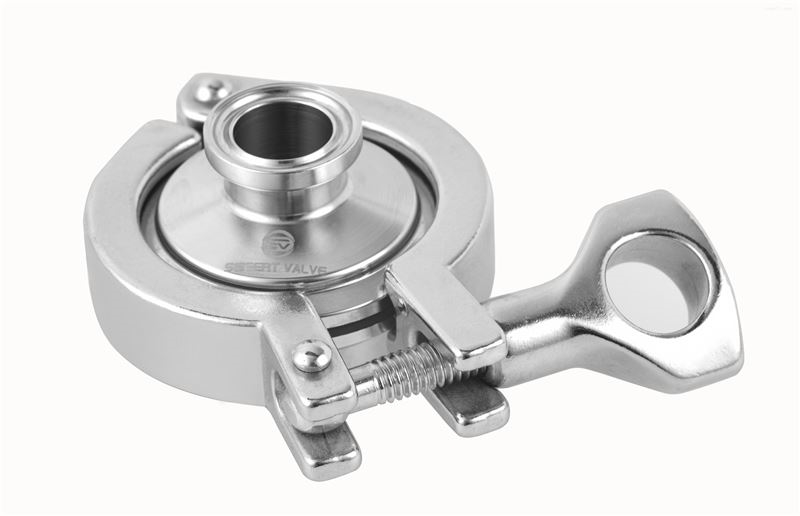
从上游细胞培养到下游制剂灌装,生物制药专用阀门正以“分子级”精度重新定义药品生产的洁净标准。随着CAR-T疗法、mRNA疫苗等新兴领域的崛起,这些阀门正向智能化、微型化方向加速进化,成为推动生物医药产业高质量发展的“隐形引擎”。